Enhance Offshore Wind Installations with Cranemaster®
- Enhanced Safety
- Operational Efficiency
- Tailored Solutions
Protection of crane and rigging during pile hammering
Reducing risk in piling operations
Sudden free fall of the piles during pile hammering due to layering in the soil, so called pile runs or pile drops, is an increasing concern in the industry. The snap loads following pile runs can be very high, exposing both personnel and equipment to high risk.
In cooperation with key players in the industry, Cranemaster has developed special shock absorbers that will reduce the snap loads to acceptable levels. As a result, risk is reduced, and expensive interruptions in the piling process avoided.
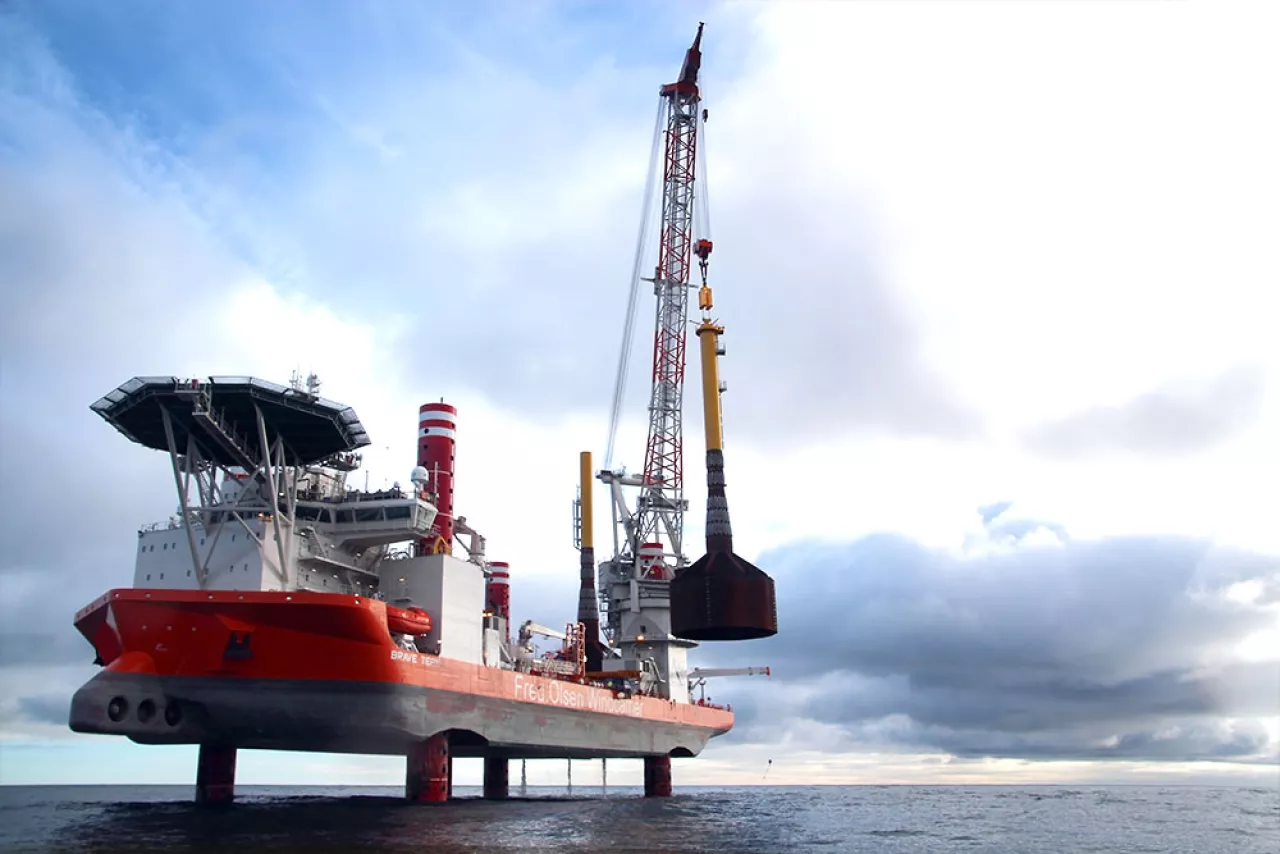
Cranemaster® Benefits
Cranemaster® delivers key benefits for offshore wind projects, enhancing safety and efficiency. With our shock absorption and passive heave compensation technology, monopile installations and lifting operations are controlled and reliable, even in harsh conditions. This reduces Waiting On Weather (WOW) downtime and helps keep projects on schedule. Cranemaster® also offers bespoke solutions tailored to the unique needs of each installation, ensuring optimal performance and reliability from start to finish.
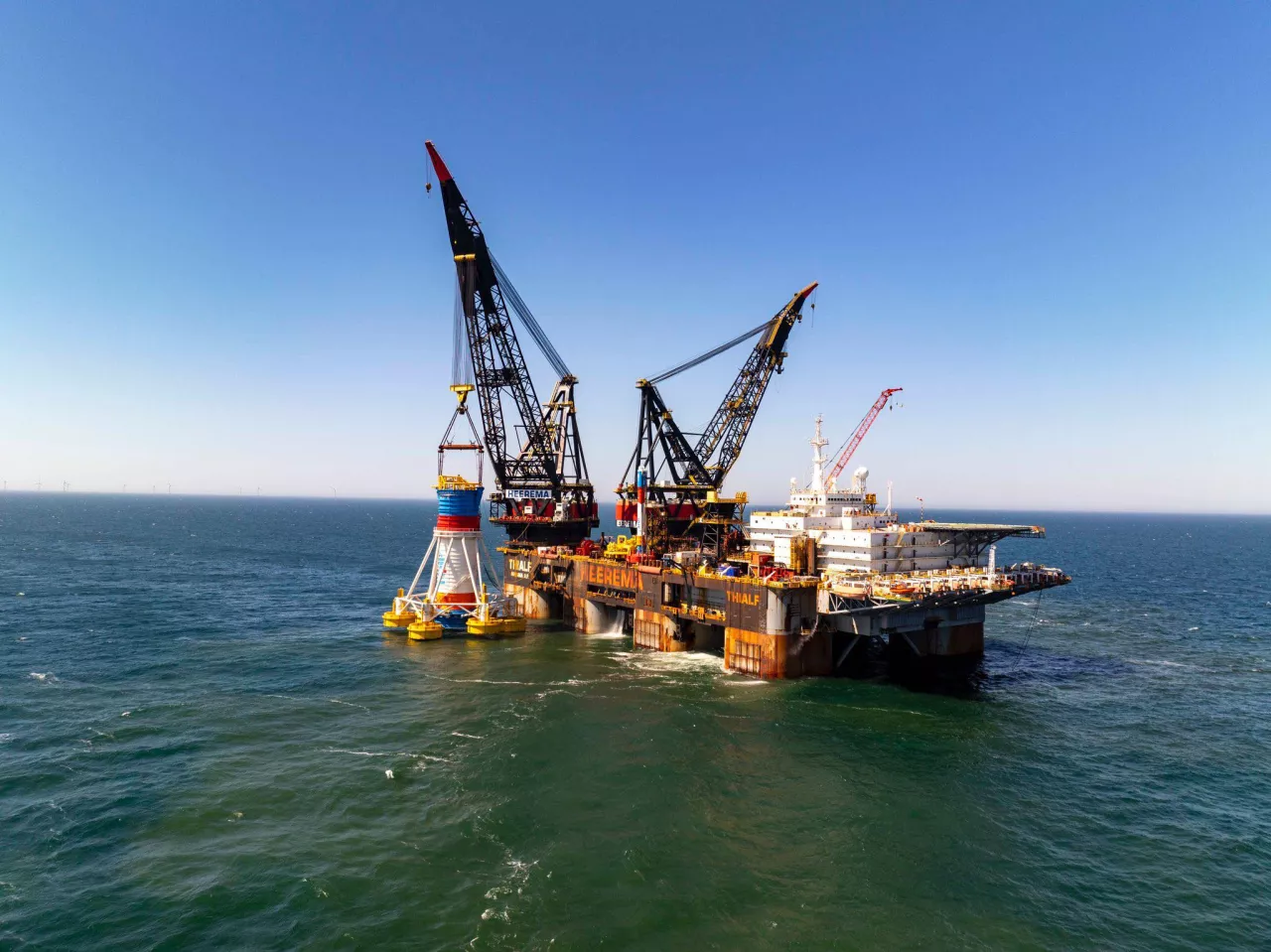
Trusted by

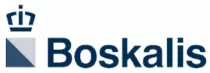

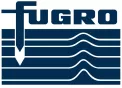
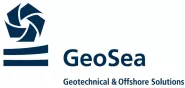
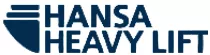

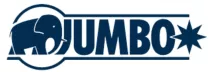
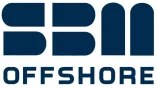
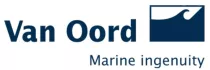
Pile Run with and Without Cranemaster
This simulation shows a pile hammer, 300 ton weight in air. The hammer falls a distance of 0,8 meter and is then stopped by the crane wire.
This Orcaflex simulation shows a pile hammer drop. The hammer falls a distance of 0,8 meter and is then stopped by the crane wire. Weight of hammer in air is 300 ton.
With Cranemaster (Left):
• Snap load = 513T
• Ringing eliminated
Without Cranemaster (Right):
• Snap load = 964T
• Significant ringing effect in crane and pile hammer
Speak with an Expert
Have questions about which Cranemaster unit is the best solution for your Offshore wind installation? Fill in our contact form and one of our experts will get in touch to discuss.
Typical Offshore wind operations where Cranemaster should be considered
Services
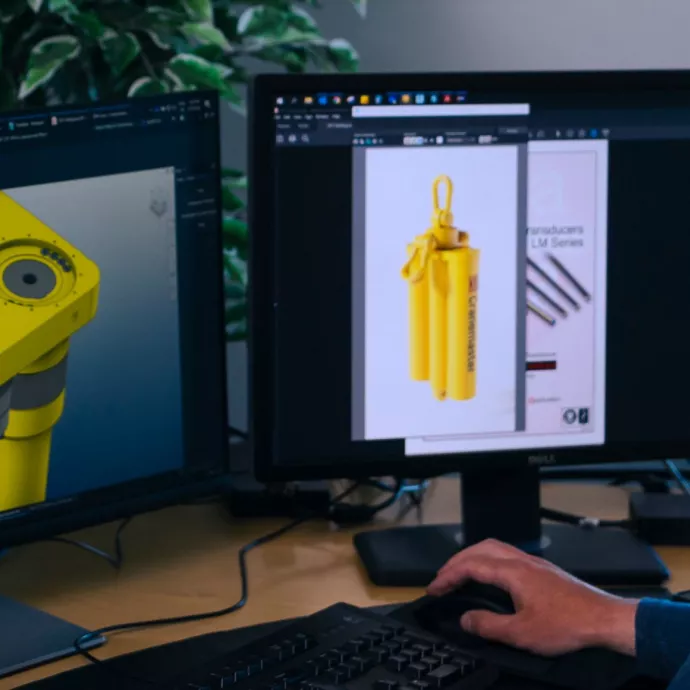
Engineering Services
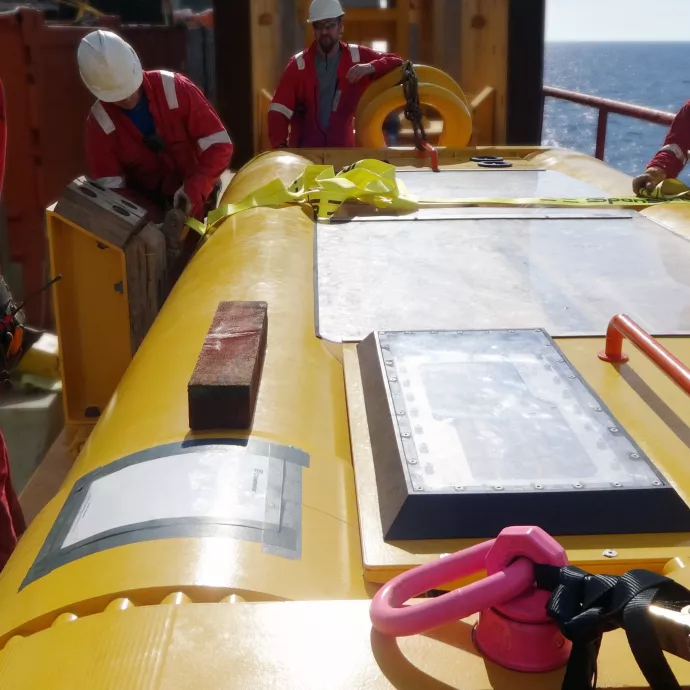
Operational support
